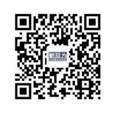
微信公眾號二維碼
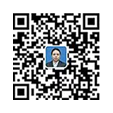
微信咨詢(xún)顧問(wèn)二維碼
新益為精益生產(chǎn)咨詢(xún)公司概述:作為制造型企業(yè),現在在市場(chǎng)經(jīng)濟的大環(huán)境下企業(yè)要有競爭力就必須在精益生產(chǎn)方面下大功夫。通過(guò)參加精益生產(chǎn)管理培訓課,我對精益生產(chǎn)的理解更為深入。下面講解我的心得體會(huì )。
精益生產(chǎn)管理培訓
一、對精益生產(chǎn)管理中七大浪費的再認識
在未聽(tīng)課前,我已知道七大浪費是:制造過(guò)多/過(guò)早的浪費;等待的浪費;搬運的浪費;庫存的浪費;制造不良品的浪費;多余加工作業(yè)的浪費;多余動(dòng)作的浪費。但只是對這幾種浪費有種模糊的概念,認識并不深刻。通過(guò)聽(tīng)課,我對七大浪費有了更深入地理解。
1、制造過(guò)多/過(guò)早的浪費是直接產(chǎn)生對流動(dòng)資金的占用,這個(gè)浪費曾經(jīng)對豐田公司造成過(guò)沉重的打擊。在1947年到1948年之間,豐田公司的新任總經(jīng)理大野耐一,將生產(chǎn)流程優(yōu)化,將產(chǎn)量大大提高,結果由于忽視了市場(chǎng)的需求量而導致大量的產(chǎn)品積壓,資金鏈被壓斷,公司瀕臨破產(chǎn)。正是由于這次教訓,豐田公司才提出了JIT生產(chǎn)理念,即“只有在顧客需要的時(shí)候,才生產(chǎn)顧客所需質(zhì)量和數量的產(chǎn)品”。
2、等待的浪費是指企業(yè)的資源彼此等來(lái)等去,而產(chǎn)生等待的因素則有很多,這其中包括設備的布置離散、生產(chǎn)計劃變來(lái)變去、生產(chǎn)不均衡、質(zhì)量波動(dòng)、物流配送不暢、內部失調、排程不當等諸多因素。
3、搬運的浪費是說(shuō)企業(yè)的內部設備不合理的布局、不合理的物流、離島式的工序和工段、離島式的車(chē)間和部門(mén),從而導致出現不斷的搬運。
4、庫存的浪費是指企業(yè)內部由于采購生產(chǎn)的周期長(cháng)準備的緩沖庫存、由于供應不佳和搬運量大導致的余量庫存、由于害怕出現問(wèn)題的安全庫存、由于計劃粗放和設計變更等原因導致的呆滯庫存。而所有的庫存都是要占用成本的,各類(lèi)成本累加約為成本總和的25%,同時(shí)庫存更易隱藏管理問(wèn)題、掩蓋管理失誤。
5、制造不良品的浪費是制造不良品后,返工修補浪費、工期延誤浪費,假如不能在廠(chǎng)內發(fā)現,則會(huì )造成更大的浪費。經(jīng)常會(huì )出現一人錯誤百人忙的連鎖反應,其成本耗費的比率為1:30:600:9000。
6、多余加工作業(yè)的浪費是指技術(shù)部門(mén)的浪費而言的,例如:零部件的數量設計過(guò)多、增加不必要的加工工序、加嚴要求、技術(shù)要求不足等。
7、多余動(dòng)作的浪費是指操作者在生產(chǎn)過(guò)程中與完成工作無(wú)關(guān)的動(dòng)作。人的動(dòng)作大致分為七級,級別越高,消耗時(shí)間越多,因此所有現場(chǎng)設施的布置都應該使操作者的動(dòng)作級別盡量降低,以節約時(shí)間。
二、對精益生產(chǎn)的理解。
精益生產(chǎn)是由日本豐田公司提出的,其原意就好比是一個(gè)人穿的一件衣服,無(wú)論大小、材料、樣式都很好,沒(méi)有一處是不合適的。傳到中國后,也有人將其譯為精細生產(chǎn)方式,這是不準確的。最后有人用一句話(huà)來(lái)概括:“在需要的時(shí)候,按需要的量,生產(chǎn)所需要的產(chǎn)品”。中國現代的生產(chǎn)企業(yè)已經(jīng)由原來(lái)的追求產(chǎn)量的時(shí)代到了追求質(zhì)量的時(shí)代,這個(gè)時(shí)代也很快就會(huì )過(guò)去,將進(jìn)入成本的時(shí)代,也就是微利的時(shí)代,當這個(gè)時(shí)代來(lái)臨時(shí),如果不能降低企業(yè)的成本,那么企業(yè)必然會(huì )虧損,最終將面臨被淘汰的局面。因此精益生產(chǎn)方式才被推到了歷史的前沿,因為在目前來(lái)說(shuō),精益生產(chǎn)管理就是控制浪費、節約成本的最好的一種生產(chǎn)管理方式。因而全世界的企業(yè)都引進(jìn)精益生產(chǎn)管理,希望能改變企業(yè)的面貌,獲取更大的利潤。
三、對精益生產(chǎn)如何整頓浪費方法的認識
對如何消除浪費,豐田公司對此有個(gè)形象的比喻,比如家里的水龍頭開(kāi)了,流了一地的水,采取的措施肯定是先關(guān)水龍頭,再拖地。但是在企業(yè)中,出現問(wèn)題,大多數是去想怎么辦,采取什么措施來(lái)解決問(wèn)題,而從來(lái)不去想為什么,這就與不去關(guān)水龍頭,而是先去拖地是一樣的道理。只要對每個(gè)問(wèn)題都找出為什么,然后再針對為什么而采取必要的措施,才能將問(wèn)題徹底解決,換句通俗的話(huà)來(lái)說(shuō),就是要先關(guān)“水龍頭”,只有先關(guān)閉亂源,才能控制住浪費。豐田公司針對七大浪費,提出了JIT的生產(chǎn)方式;并在生產(chǎn)中盡可能地集結制程,對于制程由于設備、場(chǎng)地等因素無(wú)法集結的,采用后拉式生產(chǎn)來(lái)控制浪費;通過(guò)5S管理的開(kāi)展,對現場(chǎng)存在著(zhù)的庫存進(jìn)行不斷的整改;通過(guò)運用“防呆手法”(美國稱(chēng)之為“防錯手法”)來(lái)不斷地改進(jìn)生產(chǎn)中的不合理現象、控制生產(chǎn)中出現的浪費。對這些浪費研究出控制方法后,豐田公司又提出了第八大浪費,那就是忽視員工智慧潛能的浪費,他們認為很多的問(wèn)題,工人都有很好的辦法來(lái)解決。針對此點(diǎn),豐田公司制定了一系列的辦法來(lái)充分發(fā)揮工人的參與積極性,比如,他們的工人發(fā)現改進(jìn)解決或改進(jìn)問(wèn)題的辦法時(shí),工人只需將管理人員叫到現場(chǎng),說(shuō)明自己的改進(jìn)方法就可以了,剩下的填表、申報的工作都由管理人員來(lái)執行,工人就可以拿到獎勵。他們要求每個(gè)工人每月必須有一項創(chuàng )新或改進(jìn),并且將一些好的辦法在每年底都匯總后編成一本書(shū)。
豐田精益生產(chǎn)管理就是通過(guò)這些辦法來(lái)消除浪費和不斷改進(jìn)不足,以此來(lái)降低成本,增加利潤。最后,我想說(shuō),只要能夠從一點(diǎn)一滴的小事改起,將精益生產(chǎn)管理理念逐漸地滲透于日常的生產(chǎn)中,精益總會(huì )帶來(lái)意想不到的收獲。我相信總有一天,當我們面臨生產(chǎn)計劃跟不上變化的時(shí)候,不是改變計劃,而是學(xué)會(huì )控制變化。
建立生產(chǎn)有序、管理順暢,操作規范,士氣高昂、高質(zhì)量、低成本、短交期的作業(yè)現場(chǎng);
為企業(yè)規劃設計一套由內到外的形象升級,外觀(guān)視覺(jué)價(jià)值體現、內在的管理內涵體現;
全員參與設備管理高產(chǎn)出和低成本運營(yíng),提升設備管理能力,維護能力,提高效率
構建班組生產(chǎn)管理體系、循環(huán)評價(jià)、人才育成、持續改善、績(jì)效管理、文化養成體系;
提高產(chǎn)品質(zhì)量、降低生產(chǎn)成本、縮短交期、增加利潤,讓管理更系統科學(xué),執行力更強
對工廠(chǎng)的各個(gè)組成部分進(jìn)行合理安排,以提高生產(chǎn)效率、降低成本、優(yōu)化物流、改善工作環(huán)境等